This week, German media reported a different angle on the “micro-fissures” now plaguing nuclear reactors in Europe. It seems that the risks have been known for decades. Craig Morris takes a look.
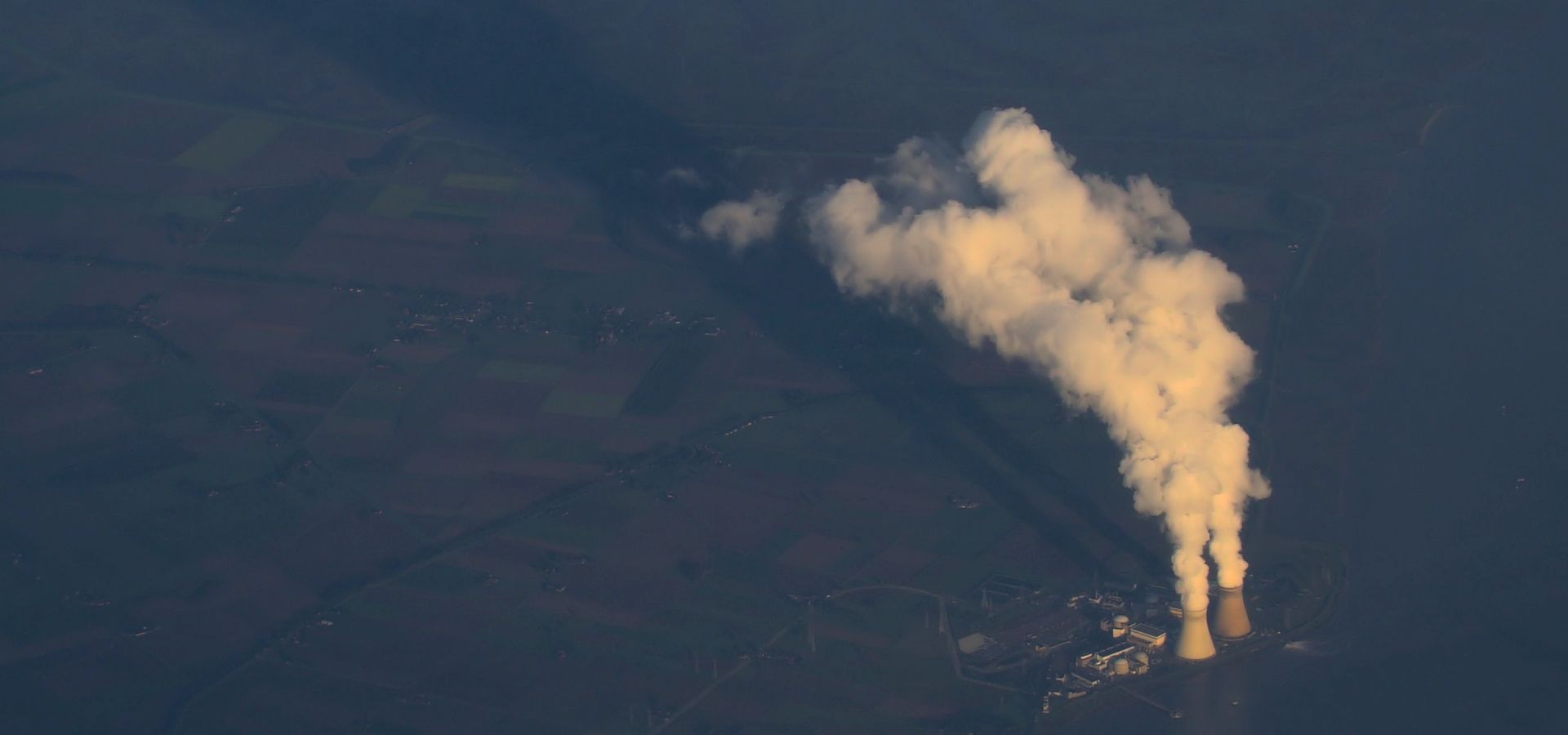
The Doel power plant, Belgium, has had micro-fissures since 1979 (Photo by Bjørn Christian Tørrissen, edited, CC BY-SA 3.0)
At present, around the third of France’s nuclear fleet is currently off-line as safety experts inspect small cracks in containment vessels. Earlier this year, we learned that improper manufacturing led to these micro-fissures way back in the 1960s—and insiders knew about the problem all along.
The issue flared up in the 2012, when micro-fissures were first (re-)discovered in Belgian reactors, allegedly because of the use of modern inspection technology. But then, a Belgian newspaper pointed out (report in German and in Dutch) that the cracks at these plants had been visible, as it reported at the time, to the naked eye in 1979, when the reactors were not yet even in operation: “In the meantime, there is no doubt that we are talking about cracks,” one politician stated in the Belgian Senate, according to a report from 29 December 1979. (In his defense, the current director of the Belgian Nuclear Control Agency, who oversaw construction of the reactor in question, says he “cannot remember” the discussion.)
Now, Süddeutsche Zeitung (in German) and WDR (see this video in German) reported that nuclear plant operators have not only known about the issue, but have even been compensating for it for decades. At 18 reactors from Belgium to the Czech Republic, France, Finland and Slovakia, the emergency cooling water is preheated to as much as 60°C. As the table below shows, the practice began in Belgium, Finland, Slovakia, and the Czech Republic in the early 1990s.
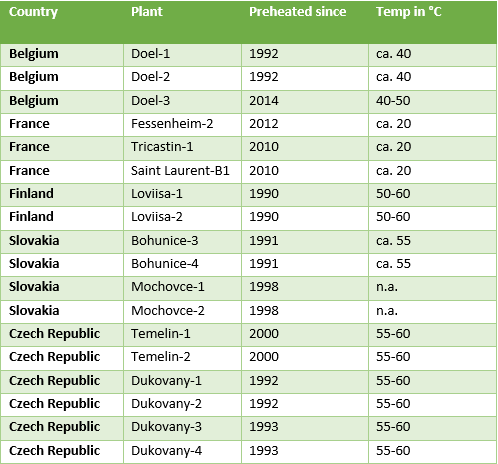
European nuclear reactors whose emergency water cooling facilities have been preheated. (Source: WDR)
The problem is that cold cooling water, which generally has a temperature of 5 to 10 °C in Europe, could cause thermal stress on the reactor wall if it is introduced quickly. If the wall already has fissures, the result could be a material failure leading to a leak. If enough of the cooling water escapes through that leak, a meltdown could be the result. In return, however, a higher cooling water temperature also reduces the cooling effect.
Not all of the reactor operators interpret the preheating of emergency cooling water as an indication of an underlying safety issue, however. A spokesperson for Czech utility CEZ told WDR, “That is not a security measure but rather the result of constant improvements,” with the goal of reducing the impact of any use of emergency cooling water “on the service life of the reactor’s containment vessel.” But not all of the companies responded to the press’s requests for statements.
For what it’s worth, the German reporters were unable to discover any such practice in Germany, and the German Environmental Ministry (which handles nuclear safety) stated that emergency cooling water was not preheated at any reactor in Germany “because of the [containment vessels’] current and expected material condition at the end of their service lives,” ending no later than 2022. (In other words, we are shutting them down anyway, so we don’t need to worry about longevity.) However, Wolfgang Renneberg, head of reactor safety at the German Environmental Ministry up to 2009, says the practice is “common in Russia and the US” as well—it simply is not reported.
As Michael Sailer, head of Germany’s Nuclear Waste Management Commission, told the reporters, the steel reactor wall is constantly bombarded with neutrons, becoming brittle in the process—even without any cracks that have been there from the beginning. These containment vessels, properly manufactured (no cracks), were designed to last for 40 years. The average age of a European nuclear reactor is now 32 years. “We are increasingly approaching the material’s limits,” Sailer warns.
Craig Morris (@PPchef) is the lead author of German Energy Transition. He is co-author of Energy Democracy, the first history of Germany’s Energiewende, and is currently Senior Fellow at the IASS.
The claim of nuclear fans that the true life of a nuclear reactor is 6o years is looking increasingly implausible. Much machinery, including aircraft, does not IIRC have a service life as such – the maintenance costs just keep rising until its not worthwhile paying them, and you scrap and replace. The USAF still flies B52 heavy bombers built in the 1950s, as it does not have a replacement for these giant bomb trucks. French reactors seem to be following this pattern.
This is sensible practice in action, not a cause for particular concern – hence why it remained ‘unreported’.
The issue of microcracking appear to be an artefact of the manufacturing process, hence one other reactor who’s RPV barrel was made at the same facility – Tihange 2 was also taken out of service, pending investigation.
What’s key is that the cracking is circumferential – that is it runs parallel to the pressure vessel wall, not across it.
Cracking is an issue in pressure bearing systems when the cracks are such that they can grow – that is, where there’s a force “pulling open” the crack. The crack acts as a stress-raiser, such that local stress/strain at the tip of the crack is greater than it is in the uncracked body of the material. If that concentrated stress is greater than the local strength of the material, the crack may grow – however, the speed of growth depends on the material – if it’s ductile the crack must “tear” the material, which is energy absorbing. The crack can then grow only slowly, if at all. If the material is brittle, then the crack can propagate quickly. If the crack encounters a formation in the metal )or other material) that dissipates the energy, or stops it concentrating stress, crack growth stops.
Stresses in a vessel under internal pressure run in such a way to try to expand the vessel at a right angle to the local circumference – which is at a right angle to the cracking observed in the Reactors. There is therefore no force acting to pull open the cracks, hence no contribution to crack growth. In fact, if there were radial cracking – which would be an issue – the circumferential microcracks would tend to act as a blocker to crack growth, as they’d dissipate stress at the crack tip, when it encountered a circumferential crack (in fact, it’s usual to use laminated vessels for some high-pressure applications for just this reason).
What’s been being gone over in detail is whether that’s the case around “penetrations” – where nozzles are welded into the vessel to allow cooling water, instrument cables etc. in and out. So far as I gather, every single one has been gone over for evidence of local cracking, and none found.
@ Nicolay
If you want to out yourself as a Troll or atom clown you have just done so.
http://deredactie.be/cm/vrtnieuws/binnenland/1.2250955
A picture says more than a funny text, doesn’t it?
Circumferential yourself at cm 22 and cm 29 ….. with a sharp lens or any other tool.
@heinbloed
“troll” ? “atom clown”?
I had no idea discussing the science was so invidious to the German coal lobby.
Thank you for the old link – it is approaching two years out of date, but even so it concurs with what I said about the cracks not growing, originating as they do from the original casting – strange as it may seem, the opinions of politicians on nuclear physics and materials science does not outweigh the scientific consensus on these issues and the scientific consensus is that radiation has no role to play in hydrogen flaking, as also confirmed in your link.
Here’s how it resolved.
http://www.world-nuclear-news.org/RS-Belgian-reactor-resumes-operation-after-vessel-inspections-1512155.html
If you want to discuss this then you should take the time to read it – and perhaps even your own link….
The context of this is, as we know, that Germany is building new grid connections to Belgium (BeDeLux interconnector) and desperately seeks to displace nuclear of its neighbours, stabilise the swings of renewable energy but most importantly, sell cheap high carbon (lignite coal derived) baseload electricity.
Placing pressure on Belgium 9and others) to close nuclear plants is in the German coal industry’s interest, but in the words of a great philosopher, ‘you can’t always get what you want’.
Sadly, Germany’s recent stall in investment in renewables, abandonment of nuclear and efforts to stabilise their grid and thereby sell the most polluting carbon electricity (from lignite) is, at the end of the day, in few people’s interest.
We all live on the same planet and we really really need Germany to stop strip mining and burning lignite coal.
Please.
https://germanwatch.org/en/download/13626.pdf
“The issue of microcracking appear to be an artefact of the manufacturing process” – oh yeah? This from the “World Nuclear association”
“For very large generation 3+ reactors, production of the pressure vessel requires, or is best undertaken by, forging presses of about 140-150 MN (14-15,000 tonnes) capacity which accept hot steel ingots of 500-600 tonnes”.
When you forge something (which I have – admittedly not using 14k-tonne press) if you end up with micro-cracks then you have done something wrong – usually the ingot will have been at the wrong temperature when it was being bashed. Forging should not generate micro-cracks – indeed quite the reverse – if there are any at the start there should be none at the end – cos – that is one of the “artifacts” of forging – the elimination of cracks, micro or otherwise.
[…] the fall of 2016, 20 of France’s 58 reactors were offline, largely for inspections. As of mid-January, most of these reactors were back online, however. The fleet’s total […]
[…] the fall of 2016, 20 of France’s 58 reactors were offline, largely for inspections. As of mid-January, most of these reactors were back online, however. The fleet’s total […]
[…] the fall of 2016, 20 of France’s 58 reactors were offline, largely for inspections. As of mid-January, most of these reactors were back online, however. The fleet’s total […]