Liquid fuel refining is big in South Africa, but it comes with a formidable carbon footprint. Local engineers are looking at how to turn the waste byproduct of our coal power stations into the source material to make fuel for cars and planes that will shrink the sector’s carbon footprint, writes Leonie Joubert.
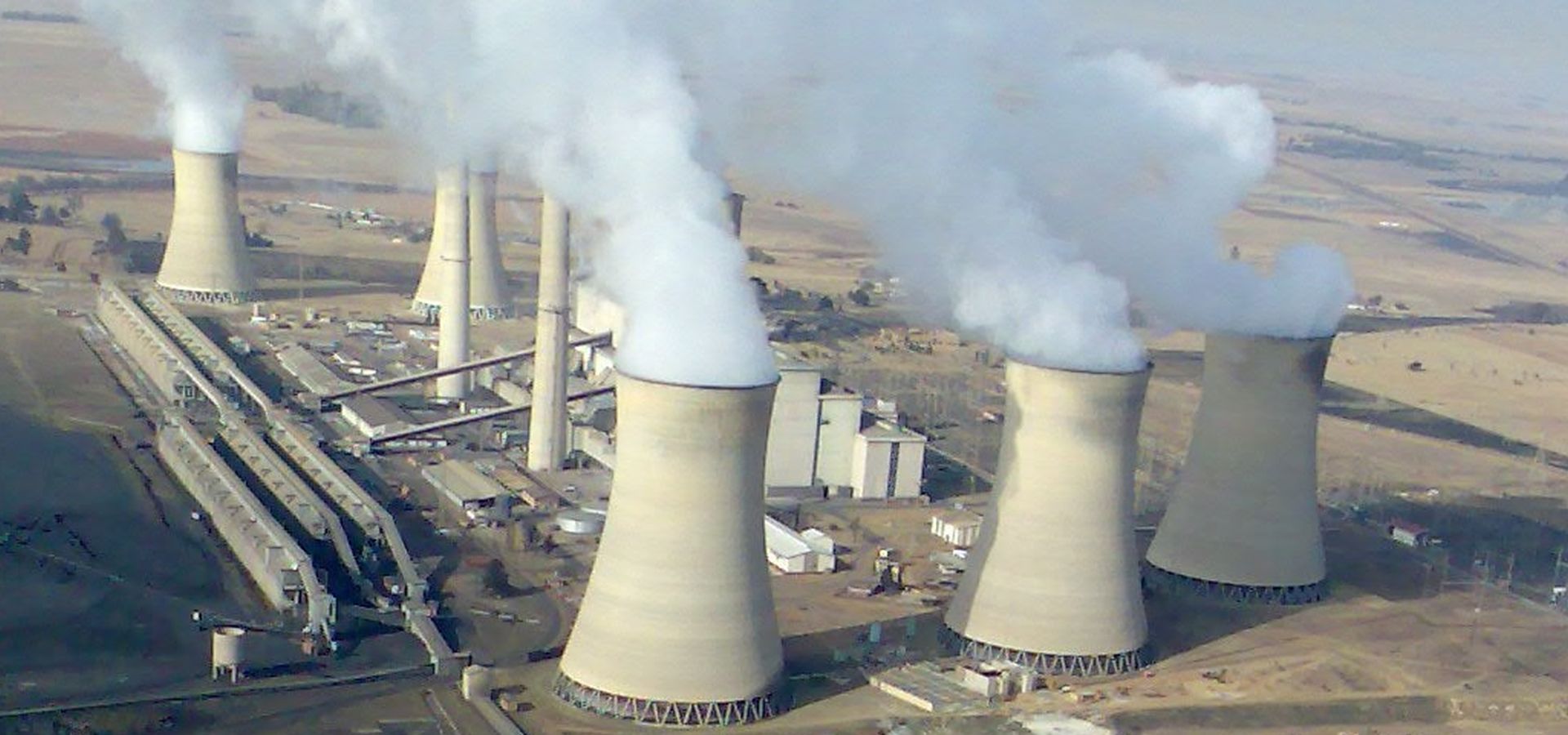
(Photo by Gerhard Roux, modified, CC BY-SA 3.0)
South Africa has two carbon emission challenges. First, the carbon dioxide from our coal power stations accounts for about half all our greenhouse gas emissions. Secondly, we’ve got one of the most productive coal-to-liquid and gas-to-liquid synthetic fuel (synfuel) sectors in the world. And while this fuel helps keep our transport sector moving and a little less at the mercy of international oil prices, it ratchets up the emissions profile of the continent’s most carbon polluting economy.
One way of dealing with the emissions from the power plants, is to catch the carbon before it leaves a plant’s exhaust pipes, pump it into some kind of subterranean landfill, and keep it locked away there indefinitely. The problem with this kind of carbon ‘sequestration’ is that it’s expensive, and it hasn’t been tested for how effective it is in the long-term.
But advances in the chemistry lab, and the boom in solar power in SA, means that this pesky carbon waste could actually be turned into gaseous gold: if it’s captured at the power station, and sold to synthetic fuel refineries, it can replace some of the mined coal or methane that are conventionally used to make liquid fuel here, and lower the emissions of the fuel and its refining process.
Most liquid fuel is refined from crude oil, explains Thomas Roos, principle research engineer at South Africa’s Council for Scientific and Industrial Research (CSIR). But in SA, our two synfuel giants, SASOL and PetroSA, make liquid fuel by putting coal (in SASOL’s case) or methane (in PetroSA’s case) through a series of thermo-chemical processes.
Making liquid fuel using these processes needs fossil fuels for two reasons: you need the source material, or ‘feedstock’. This involves mining ancient coal or methane, which are then refined, turned into a consumable fuel, and then burned in a car or plane engine. There are emissions associated with mining the fuel, and then emissions as this fuel is burned to power the plane or car.
Secondly, though, the refineries need to burn additional fossil fuels to generate the heat needed to drive aspects of the refining processes.
But as Roos explains, advances in thermo-chemical and electro-chemical processes, and the solar energy boom here, means there may be ways to significantly reduce the overall carbon footprint of this fuel.
One process could involve capturing a coal power station’s CO2 waste emissions and using it as the feedstock for the liquid fuel, instead of mining coal to feed into the refinery. This process can also use renewable solar PV electricity to drive a key refining process (involving electrolysing steam and CO2). Even though the final fuel product is still burned to produce carbon waste, at least some of the coal stays in the ground, and the refining process produces fewer emissions.
Air travel needs cleaner fuel
The aviation sector doesn’t have as many alternative fuel options as ground-based transportation has. As the CSIR’s Thomas Roos points out, we can lower the carbon footprint of terrestrial travel by switching to public transport, or electric vehicles charged by renewable energy plants, or we can walk or cycle. But flying doesn’t give these options. So lowering the carbon footprint of liquid fuel through this sort of technology might be a way of keeping planes in the air as global demand for the sector’s reduced emissions grows.
A second process involves using CO2 to ‘reform’ methane (a complicated part of one refining process), where the heat for the refining can come from concentrated solar heat. This way, 60 percent of the methane that we would otherwise mine, stays in the ground, and the refineries heating emissions are also reduced.
Doing this, we would be reducing the emissions in three ways: we’re capturing waste emissions from the coal power plant, instead of dumping them into the atmosphere; we’re leaving some of the ‘feedstock’ of coal and methane in the ground, that would otherwise get burned and put into the atmosphere; and we’re reducing the emissions associated with producing the heat needed to make the refineries run.
The timing is just right: aspects of this technology are being tested at bigger scales; the financing mechanisms to pay for building industrial sized plants have been tested with utility-scale renewable projects, giving investors more confidence; and changes in EU regulations regarding cleaner liquid fuels mean a sure-fire market for our product, come 2020. (By 2020, 10 percent of all land-based transport in the EU must run on renewable fuel, and only 7 percent of that can come from biofuels. This means that at least 3 percent of EU’s liquid fuels must come from sources such as the kind of cleaner synfuel that SA could be producing.)
If we go this way, it could be a win-win-win: our national utility, Eskom, would get to turn its carbon waste into a sellable commodity. Instead of dumping this waste into the atmospheric ‘landfill’, the refineries would instead recycle it, and thus leave a considerable amount of coal and methane in the ground. And the emissions associated with burning fossil fuels to drive the refineries would be cut dramatically too.
Delighted to see this. I am currently in the process of doing a different system- of carbon capture to fuel which is much more energy efficient than what is described here. We will be retrofitting the combined heat power, combined – anthracite- and garbage incineration plant at Oberföhring, Munich Germany- which will be producing over 6000 barrels, 957.000 liters of finished aviation fuel, gasoline, or kerosene per day, giving municipally owned SWM-Stadtwerk Muenchen extra income after the system amortizes in only three years. The pipeline for captured carbon to gasoline and diesel will be going to the Ingolstadt refinery. The pipeline for captured carbon to aviation kerosene will be going to Munich Airport, a major European hub like Frankfurt and Berlin.
After the scale model systems prove feasible, and reliable, and cost effective, the German Bundestag – committee on energy and economy headed up by Sigmar Gabriel will draft legislation mandating carbon capture to fuel retrofits to all garbage incineration, and lignite, and anthracite power plants in Germany that are intended to stay on line during the “Energiewende”. The Europeab Unoin will mandate carbon caoture to fuel
Beautiful article, because I am now in the process of drafting and submitting preliminary patenting for the “ultra-efficient'” carbon capture to fuel system- to the German patent office. Sorry I can´t details as to how it works until the preliminary patent applications (Gebrauchsmusterschutz) applications are in.
[…] Africa has no crude oil reserves and imports 80% of its fuel. It also uses coal-to-liquid (CTL) and gas-to-liquid (GTL) technologies to produce significant amounts of […]
[…] Africa has no crude oil reserves and imports 80% of its fuel. It also uses coal-to-liquid (CTL) and gas-to-liquid (GTL) technologies to produce significant amounts of […]
[…] Africa has no crude oil reserves and imports 80% of its fuel. It also uses coal-to-liquid (CTL) and gas-to-liquid (GTL) technologies to produce significant amounts of […]