For the global construction industry, concrete is a key component. Even were only renewable energy sources employed for its production, the chemical process emits significant greenhouse gases. Paul Hockenos reports from Prague where the upcycling of waste-site rubble for new buildings cuts demand for concrete – and thus for energy.
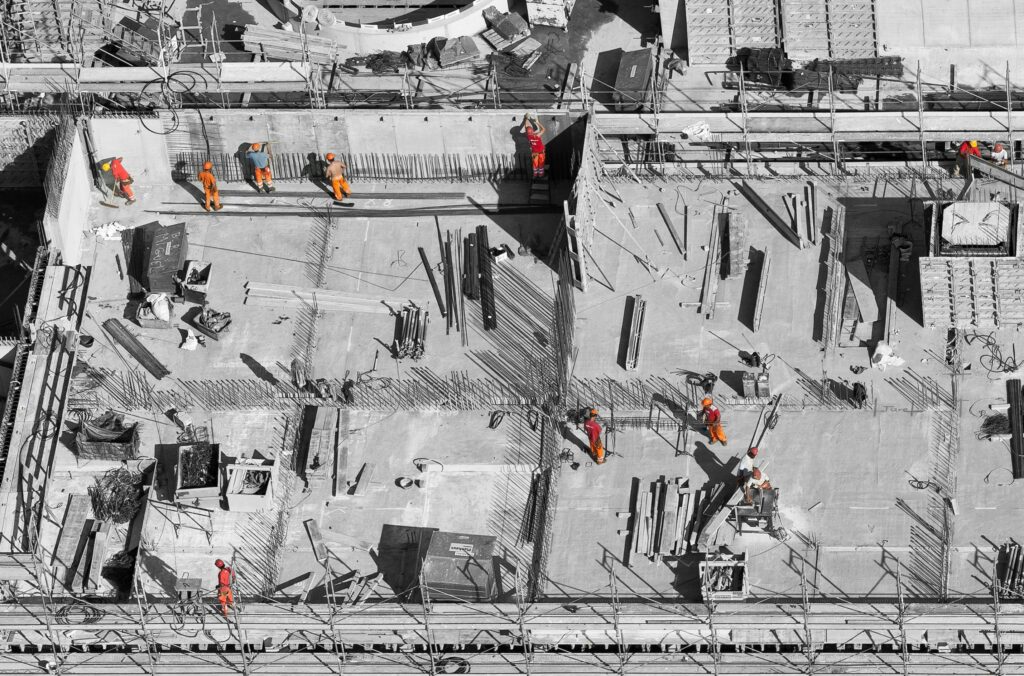
(Photo by Ricardo Gomez Angel on Unsplash)
The global push to address the sustainability of the buildings and construction sector stems from its staggering discharge of greenhouse gases – 37 percent of global emissions – and mind-blowing consumption of natural resources: half of all raw materials that humans extract from the earth’s crust find their way into buildings and other structures. Moreover, construction generates 30 percent of total refuse globally.
In terms of environmental impact, concrete itself is a particularly ignominious culprit within the construction sector, notorious for its sky-high carbon footprint – its production makes up 8 percent of global CO2 emissions – and profuse use of water, energy, gravel, and sand.
There’s no getting around the sprawling construction sector if Europe, and the wider world, intend to hit climate targets, explains José Mercado of the German Energy Agency (DENA), a Berlin-based clean energy institute. ’Even though construction’s environmental impact is so huge, there’s going to be a lot more construction happening in Europe and everywhere in order to make the building stock properly energy efficient,’ he says, noting that the EU recently doubled its energy-renovation target for buildings.
‘This is a condition for decarbonisation and reaching net zero,’ Mercado says, referring to a state in which greenhouse gases are balanced by their removal from the atmosphere.
There are a plethora of innovations and experiments in progress to limit or replace cement – the chemical substance that sets, hardens, and adheres to other materials to bind them together and make concrete and other masonry. As for concrete, half of its emissions stem from the fossil energy used to make it and the other half from the CO2 that escapes during the chemical transformation involving cement. There are a range of ways to cut this down: from adding baking soda to building construction models to concrete-like substances that require no cement at all.
And then there’s the recycling of used concrete.
One of the pilot projects exploring this path is in the Czech Republic where a demolished 19th century sugar factory is being turned into modern apartment buildings – one of five pilot projects deployed across Europe as part of the four-year CIRC-BOOST programme funded by the EU’s Horizon Europe Programme. The function of the pilots is to demonstrate, at large-scale, novel and integrated solutions for demolition, construction waste processing, management, and valorisation in new products.
The location along the Vltava River will eventually accommodate seven buildings with 790 apartments. Each new building will have ever more of its structure built out of rebetong, an upcycled brand of industrial-quality concrete developed by the Czech branch of the Sweden-based construction and development company Skanska, and turned into buildings with the help of the Prague- and London-based architecture firm CHYBIK+KRISTOF and the Czech Technical University in Prague.
The circular economy
Skanska’s rebetong is one brand of recycled concrete that, in contrast to ordinary concrete, substitutes finely crushed concrete, bricks, ceramics, and tiles for the freshly mined limestone or other rock excavated from quarries and sand borrow pits. Its perks: not only are concrete’s most voluminous ingredients replaced through upcycling, but landfill sites, the resting place of much demolition refuse, are also spared. Moreover, the highly porous nature of recycled concrete endows its end-products with better insulation properties than conventional concrete.
The practice of reusing masonry debris, among other materials such as recycled glass, as an ersatz for concrete is not new. In many places, concrete made from recycled masonry is standard for making asphalt and pavement. The drawback has long been that this kind of mixed-material concrete has proven less durable and flexible than standard concrete. Its lifespan was about half as long (roughly 30 years); being more porous, moisture penetrated it at a rate much higher than traditional concrete, causing it to crack. In the postwar period, hundreds of schools in England were built with repurposed concrete, only to suffer deficiencies and be condemned decades later.
Rebetong, however, says Skanska’s Bob Slansky, one of its creators, is in another league, a consequence of a nano-scale binding additive that boosts the product’s robustness and weather-exposure resilience. ‘Years of tests show that even with very high proportions of recycled materials, up to 100 percent, the final concrete mixture exhibits a similar performance to conventional concrete for some applications,’ says Slansky. He notes, however, that the recycled product, because of its lighter weight, is less elastic than conventional concrete and thus, at its present development, cannot completely replace it on building sites such as that of Prague’s sugar factory estates.
The on-site application of rebetong at the sugar factory estate delivered overall positive results, but also one setback. When Skanska first started with its application rebetong hardened more slowly than conventional concrete in cold weather, which put a crimp construction last winter. The crews had to lay down their tools to wait for it to dry, costing the project. Since then, tweaking produced a product that now hardens at the same rate as conventional concrete.
Another hitch is the acquisition of high-quality recycled masonry. The demolition-site debris usually chucked into landfills is often so mixed in with other materials, limiting its value for upcycling. Better recycling centers and markets for used construction materials, says Mercado, are critical to the circular economy that Europe wants to create.
‘We have to look at the entire chain of production,’ Mercado says. ‘This means the planning, the mining, and cement’s formula to transportation and more sophisticated recycling methods,’ he says. ‘It’s all one. The greatest hurdle is getting everybody on board to think about construction in a completely new way.’
The views and opinions in this article do not necessarily reflect those of the Heinrich-Böll-Stiftung European Union.